Working Questions:
I want to gain the knowledge of starting your own studio in New Zealand and how that would differ from my knowledge of studios in the US.
- What skills do I need to develop to become a well rounded maker in a professional space after graduation?
- How can I leverage my current knowledge to be an asset to a new team?
Week 1
Day 1: Monday May 24th
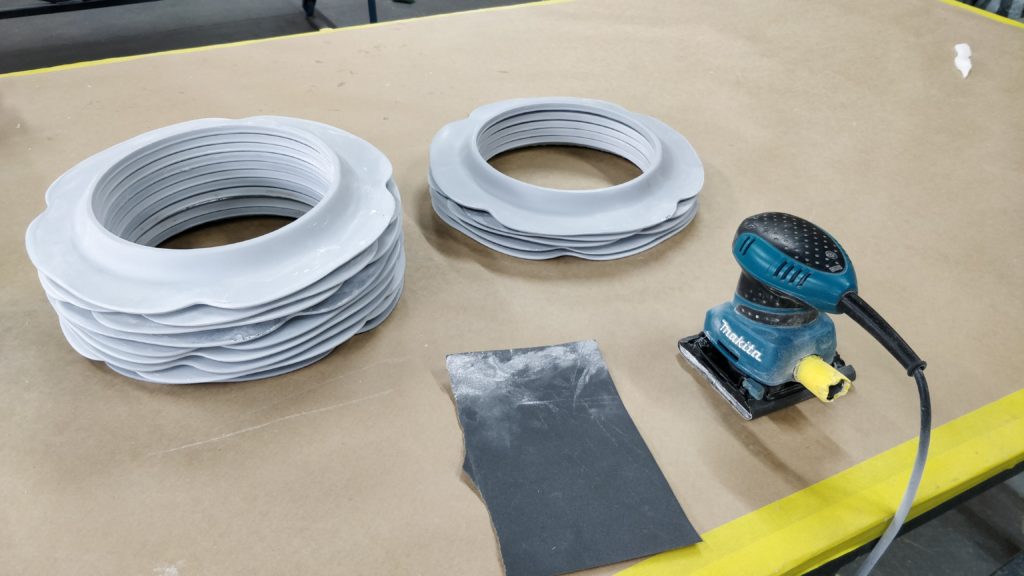
- Superglue (CA Glue)
- Baby Powder or Talc
- Flat material to mix on
- Popsicle stick or skewer
Pour the Baby Powder/Talc on the work surface then pour a small amount of Superglue in with the powder and mix to thicken and make a milky colored runny paste. This can then be used to fill in air bubbles and build up small areas quickly because of the speed the Superglue dries. With the powder mixed in it helps thicken it to be able to build up in more specific areas and use less Superglue overall.
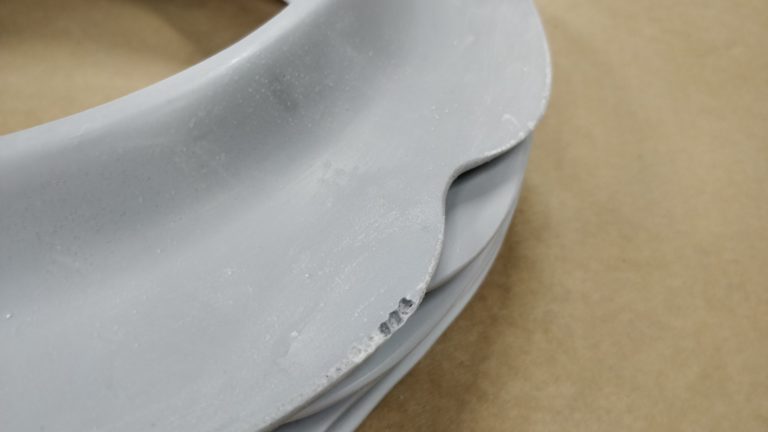
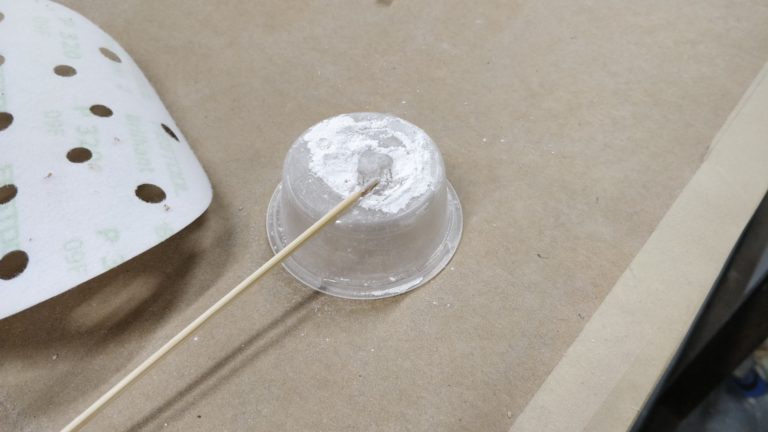
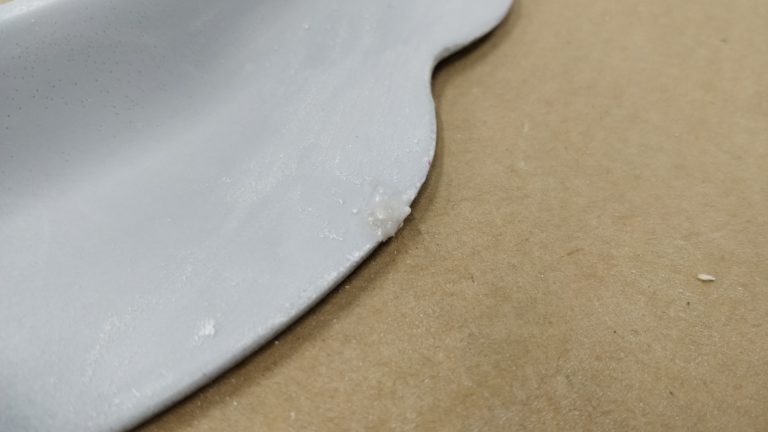
I continued to do the above steps then sanding dried parts till smooth for almost the entirety of the day. After the the casts were finished being cleaned up it was mid afternoon.
Sam and Joaquin had started on some plaques for the crew of two films they helped work on. The plaques were going to be given as a thank you for picking Scale to create some of the props. Myself and McGregor (Another employee at Scale) jumped on with them to help finish them before the day was over. Joaquin had already created the wood backs, stained them, and laser etched a thank you on the back. Our Job was to epoxy a sculpt on the front along with a cast pearl. The goal was for all of them to look the same however because they were put together by hand some looked better then others. The best ones were picked out and put in a separate pile to give to the heads of the production teams.
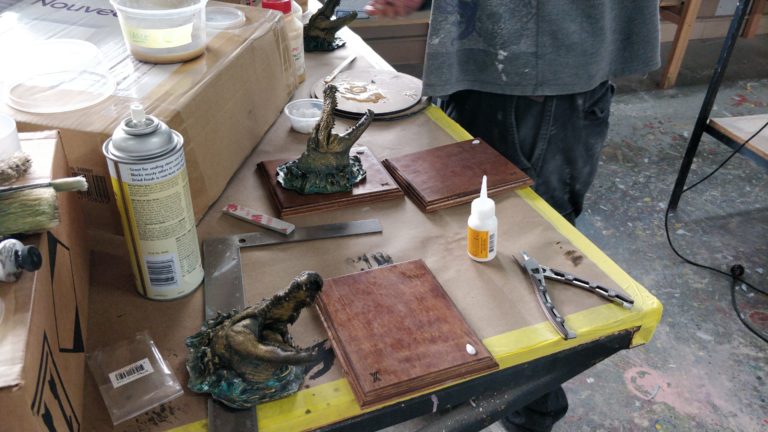
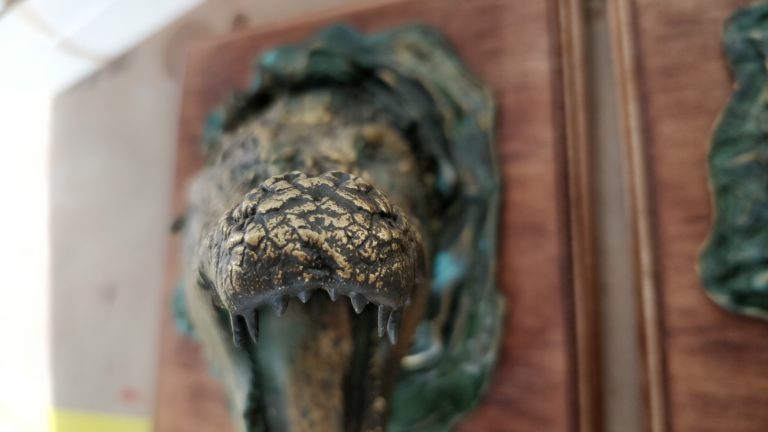
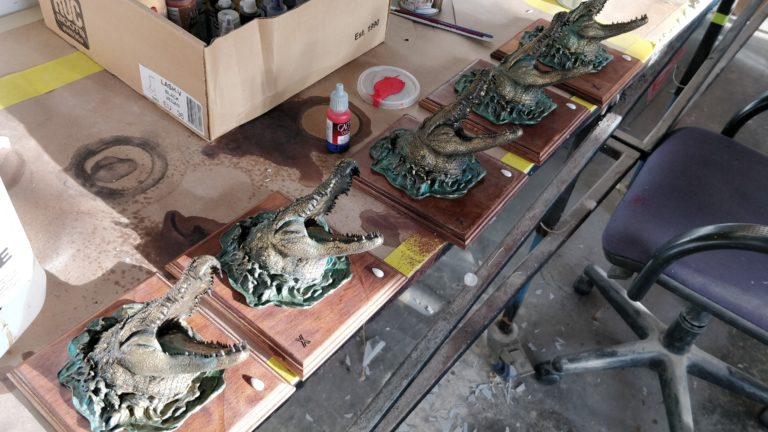
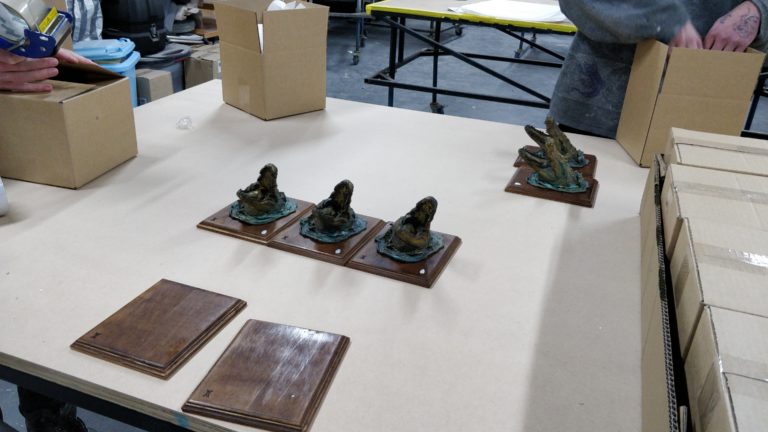
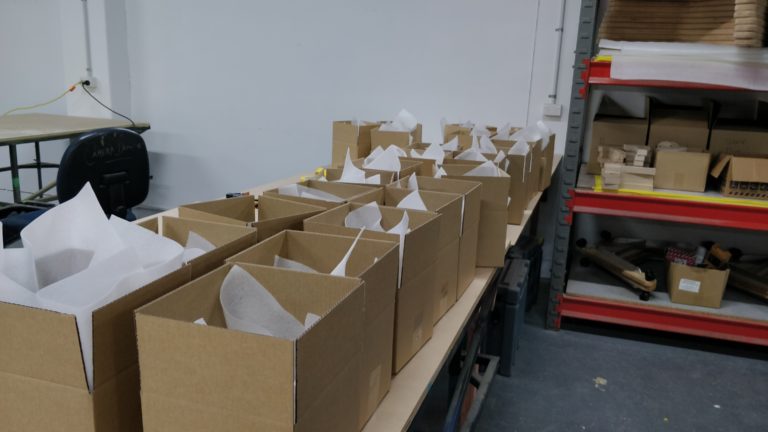
Day 1 Reflection:
- Learned new technique to use for quickly filling in small imperfections
- Started to build a connection with the team at Scale
- Saw everyone be on a level ground when it comes to completing a job together
Day 2: Tuesday May 25th
Day 2 started strong with me not having my PPE. I left school the previous Friday without it and forgot to ask someone to grab my things for me to bring Tuesday. Luckily it was not the end of the world, but it did keep me from doing things that would require a respirator.
Before lunch Joaquin also started me through the safety briefing for Scale Studios, which continued into the afternoon. We went through all the safety protocols, the SDS books for material info, as well as a tour of Avalon. It was extremely informative to understand how a business structure’s their safety briefings, and position information for incase of an emergency. There is always a booklet at the main entrance to Scale indicating the potential hazards and areas where chemicals are stored so first responders are aware of the danger areas.

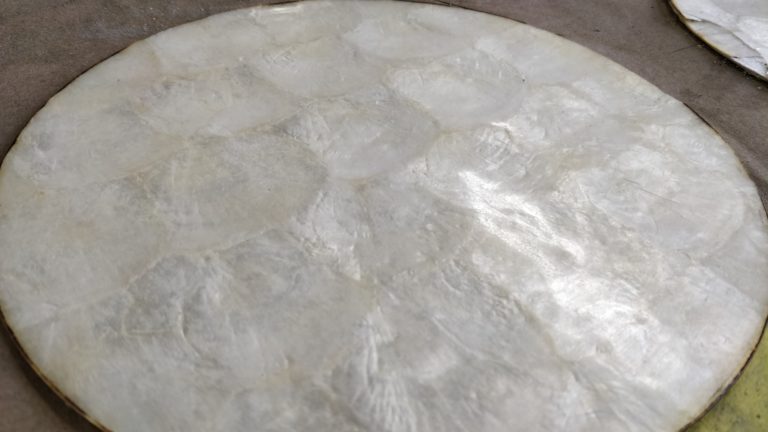
After the pearl circles were cleaned I started cleaning up the different areas of the shop. There were not many more projects in the pipeline for me to assist on at the time and the shop needed a tidy up. After as much of the dust as I could get was swept up I took over from Cody in sorting the giant, and I mean giant, collection of bolts/stuff given to Scale from previous places. That was my main focus for what was only the last hour or so of the day.
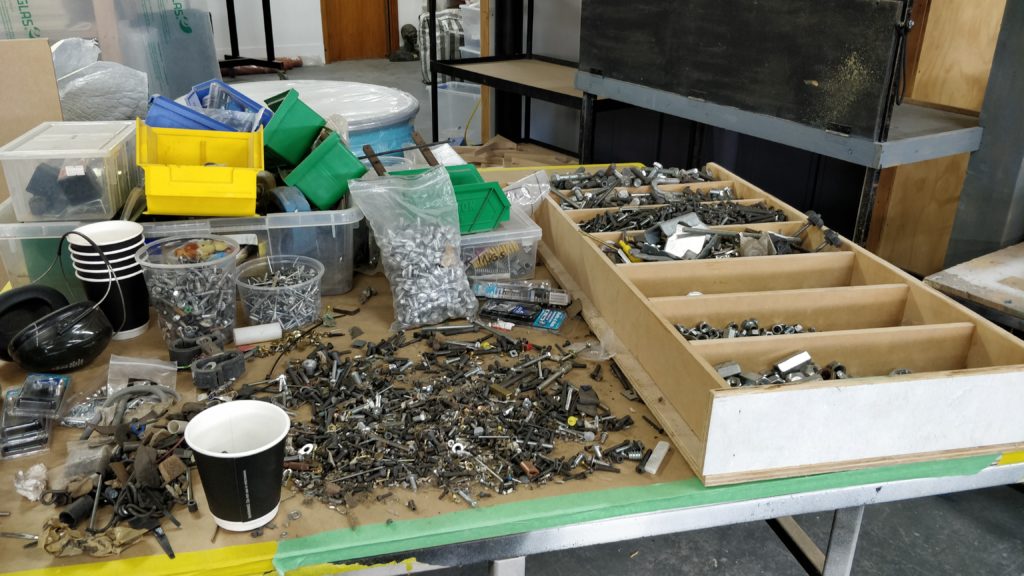
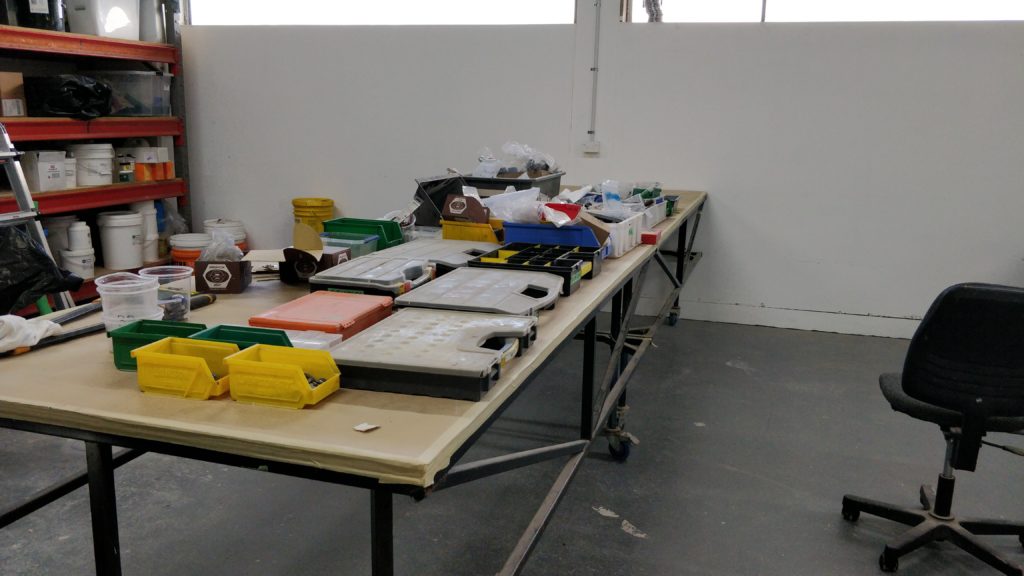
- Always bring your PPE with you for a job
- Safety Data Sheets should always be in an accessible area for quick reference
- You can use the info on Safety Data Sheets for also checking material compatibility when using paints or sealants
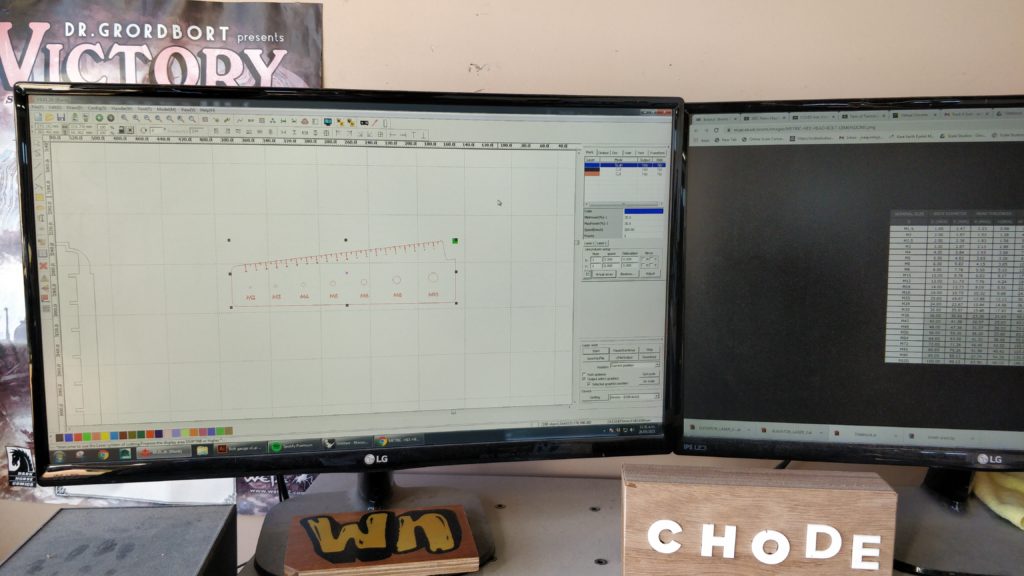
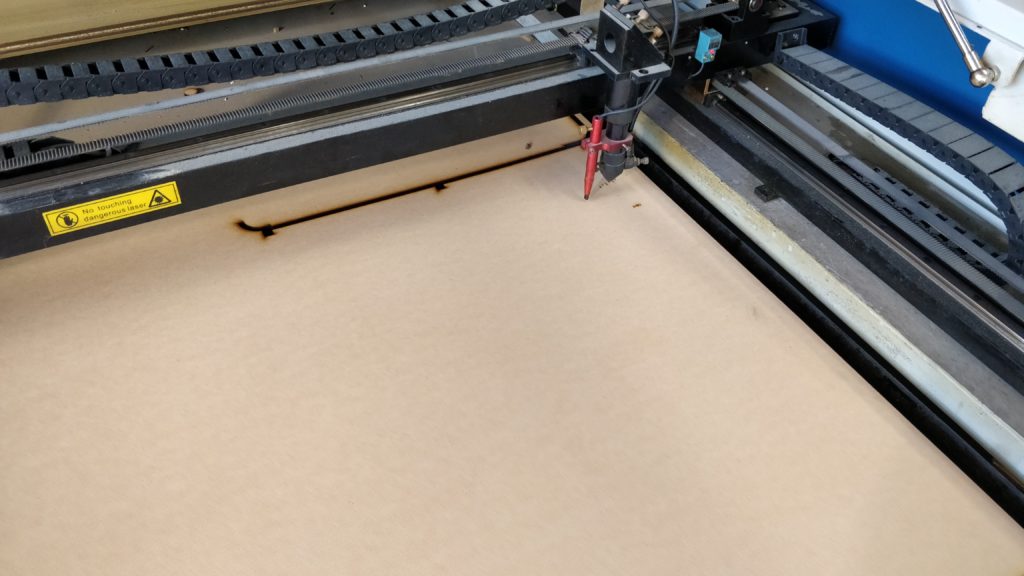
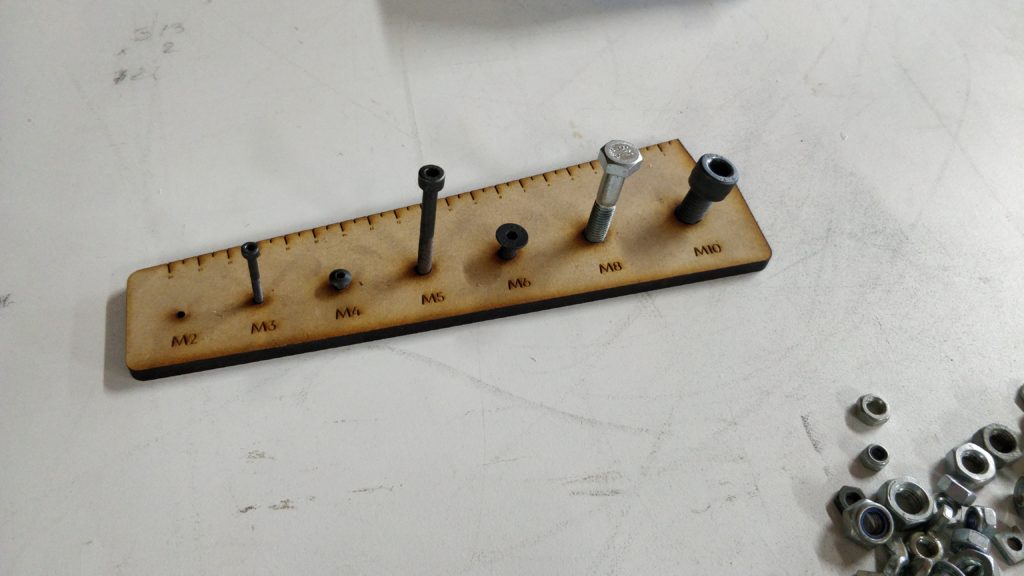
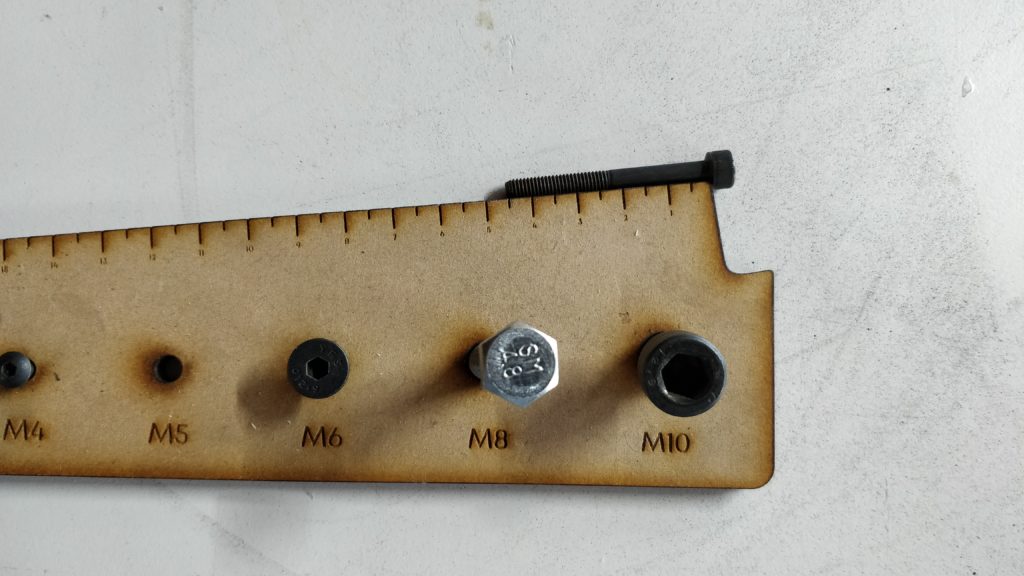
Day 3 Reflection:
- Jigs are a lifesaver in speeding up processes even if it takes time to create the jig
- When working a repetitive task it’s important to keep good posture and keep your energy up with food/water and music
Day 4: Thursday May 27th
Robbie was in the shop working on some CNC parts for a commissioned piece. He has a background in prop engineering and running CNCs so that is him main job from my understanding at Scale. The day started with him running me through on the wood CNC they have since my previous education is also in CNC engineering. The CNC at Scale makes the one at Toi look like a toy. Robbie walked me through leveling the tool to the bed of the machine before running a part and an overview of the three tool heads. For their machine they level to the bed versus the top of the material for higher accuracy since the bed is a constant flat surface. They always make sure they have a smooth sacrificial piece if they are ever cutting below the bottom of the work piece for higher accuracy across the part.
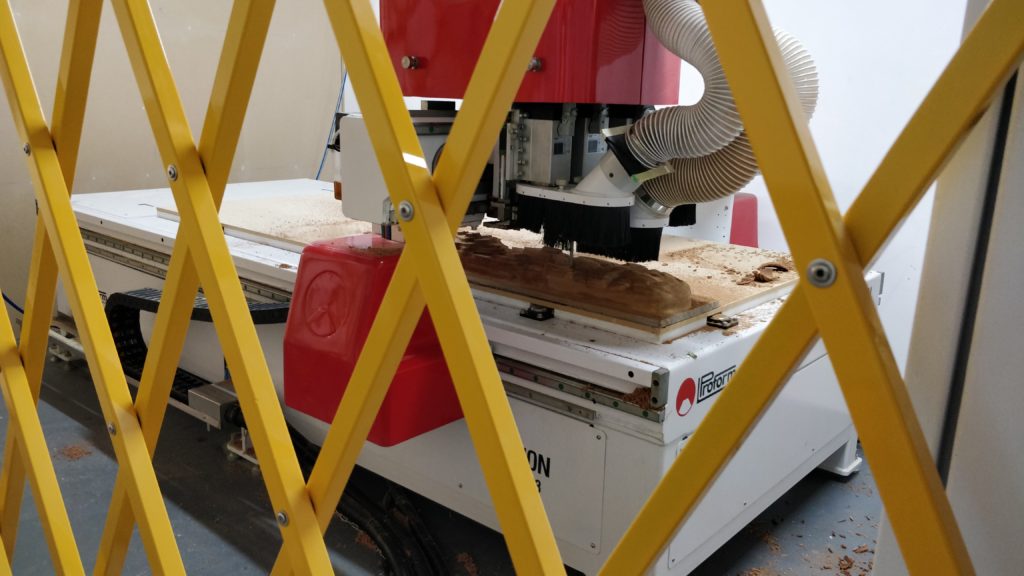
I then spent the rest of the morning and beginning of the afternoon laser cutting parts of a prop for (REDACTED). This was cool to use a laser cutter almost twice the size of the one at Toi that I’m used to. Even though it was larger it was still incredibly accurate which surprised me. I did run into some problems with laser cutting some plexiglass by accident which had really ugly marks and uneven cuts making them unusable. Besides the plexi the only other issue I ran into was some pieces broke at thin areas as they were taken out so I had to cut them a few times to make sure they were completely cut through and carefully remove them.
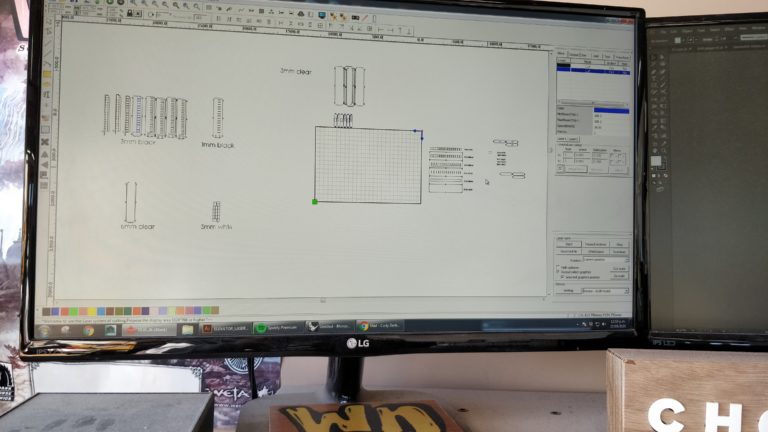
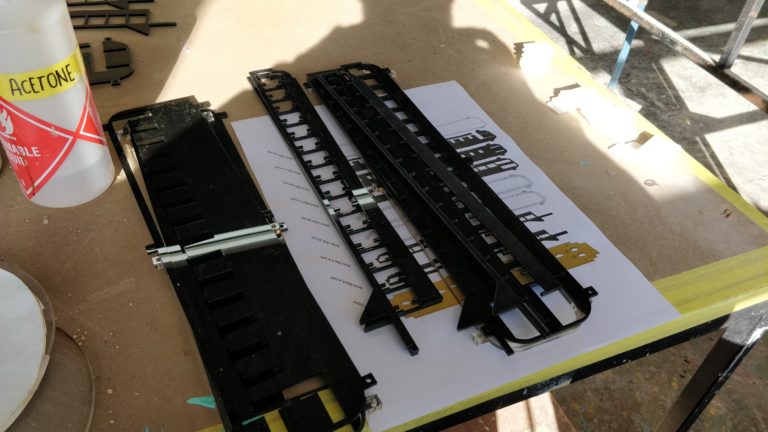
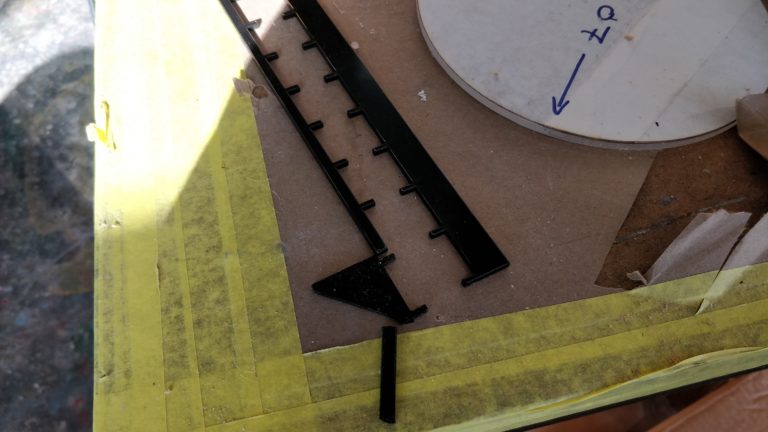
Cody took over from me at the end and I was asked to help McGregor with casting some of the last plates that were needed before they could all get primed/painted. This was super cool since Scale has all the molding/casting large equipment you could need. However their “Goo room” as they call it is SUPER hot inside. They have the combination of a heated cabinet, two space heaters, and large windows facing the sun all day keeping the room very toasty. It is on purpose though. They keep the room warm to help silicone and resins cure faster so they can be more efficient in time and not spend any more time then necessary on getting casts out.
I was assisted for the first batch then McGregor left me to do the rest while he started on cleaning up the finished casts. We still had 16 casts to go so I got to pumping them out for McGregor to sand. When the last casts finished I joined him out in the shop and we finished smoothing out the casting lines so they would be ready for priming the next day.
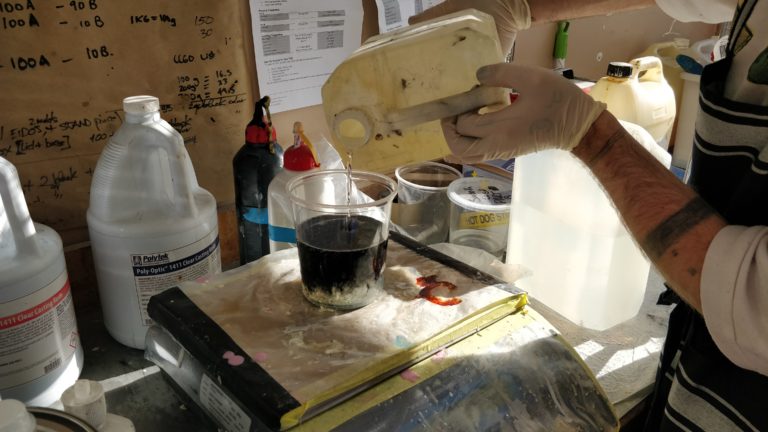
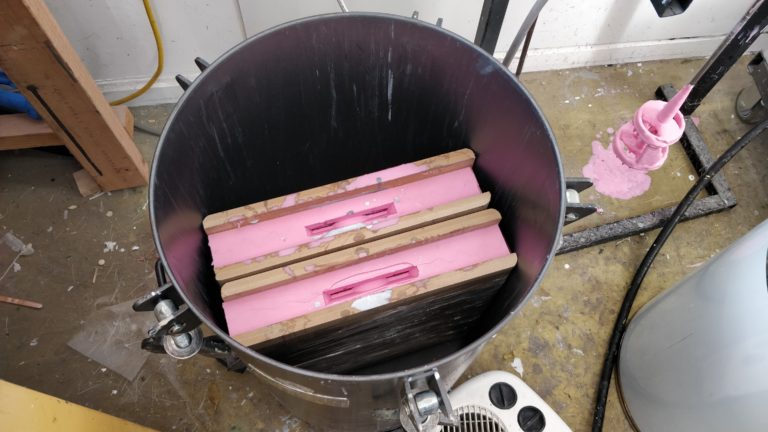
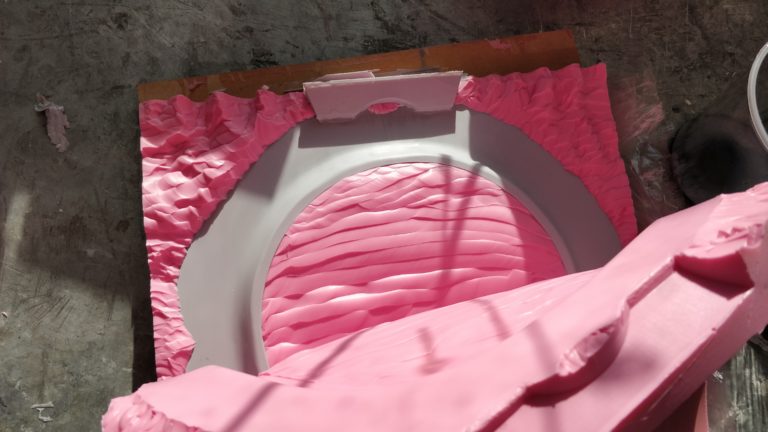
Day 4 Reflection:
- Always double check the laser will cut through on first pass so as not to mess up parts
- Double check materials before throwing them in to get cut
- Speed is necessary when casting but not in the name of not following proper steps
Day 5: Friday May 28th
The end of my first week at Scale started with gluing up some new paint stands that had been laser cut a day before. They were simple rectangles with cuts to slide together before hot gluing. I got to use Joaquin’s fancy 3M hot glue gun and I can understand why it costs so much. It’s the smoothest glue gun I’ve ever used.
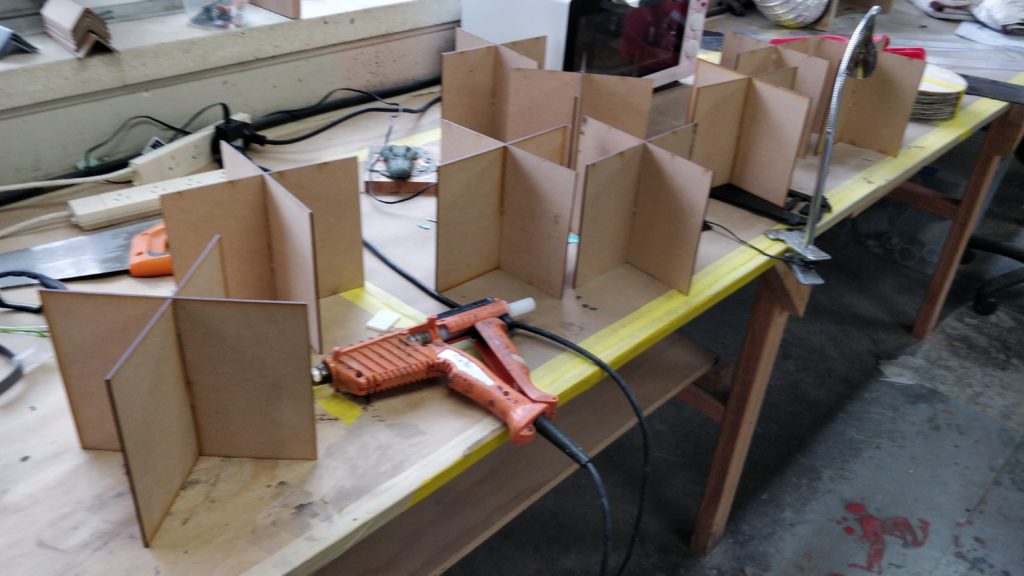
After the paint stands were put together McGregor and I took the last 18 casts down to join the other 58 casts in the spray booth. From the pictures you can tell the spray booth is HUGE. Everything was laid out on tables and the floor with room the spare. They were using DNA custom paints for the layers after a spray primer was applied. The other 58 casts already had been primed and prayed with the gloss black before we added the last 18 to the booth.
Layers applied
- Rattle can spray primer
- Gloss black (DNA paint)
- Gloss clear coat (DNA paint)
- Gold Chrome (DNA paint)
Allowing for coats to dry before the next layer we only got through the clear coat before the day was over. McGregor would be coming in over the weekend to finish the gold chrome layer so they would be done for Monday.
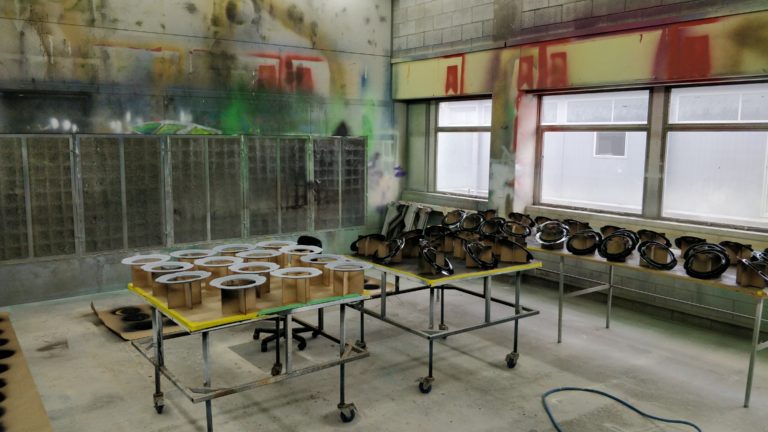
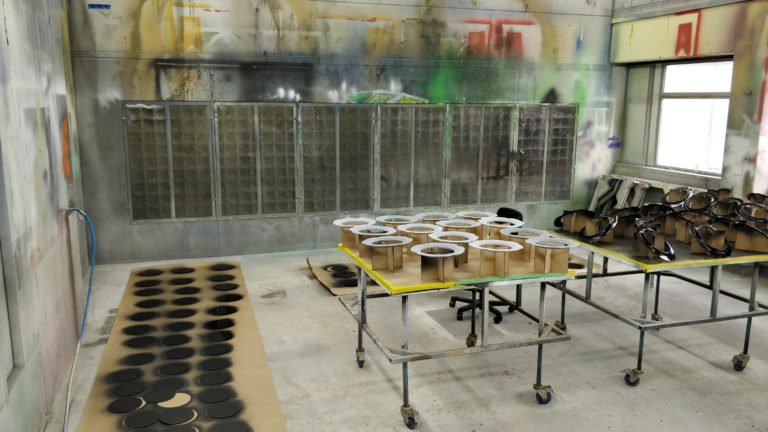
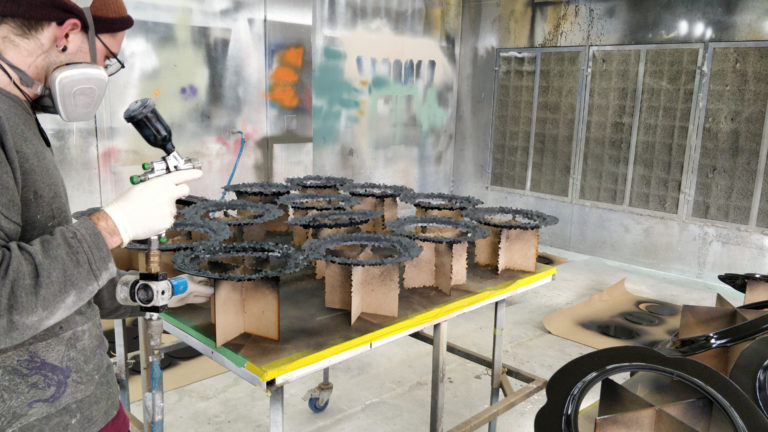
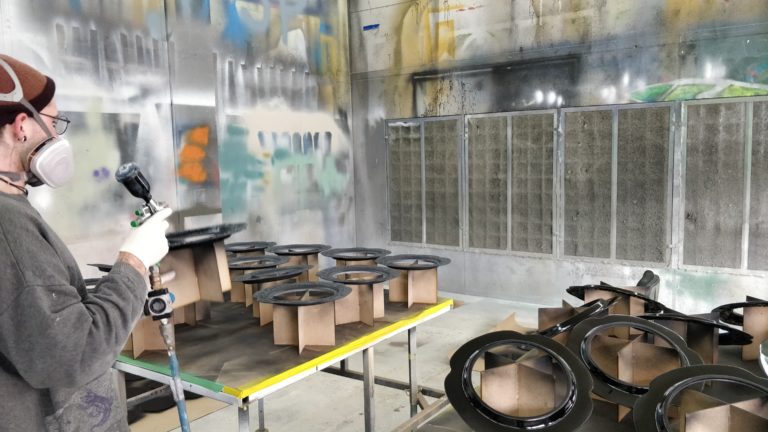
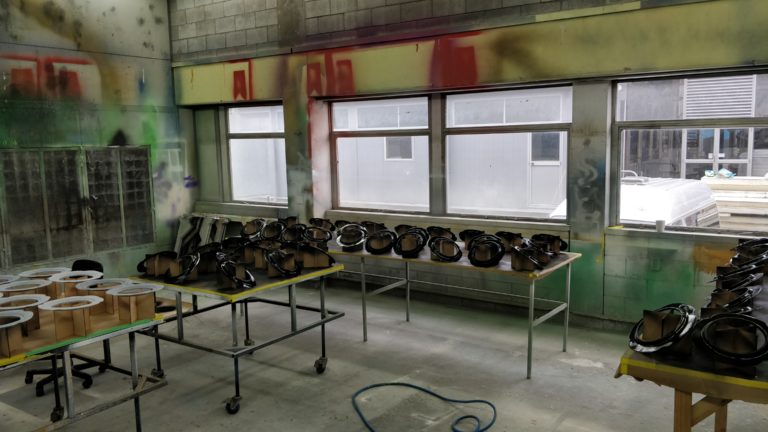
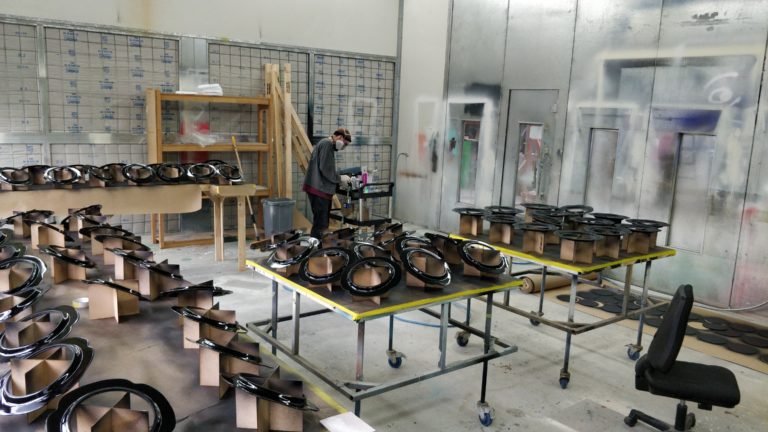
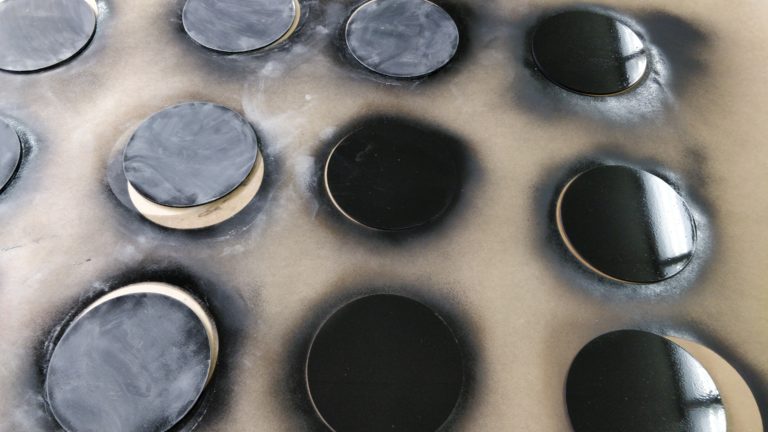
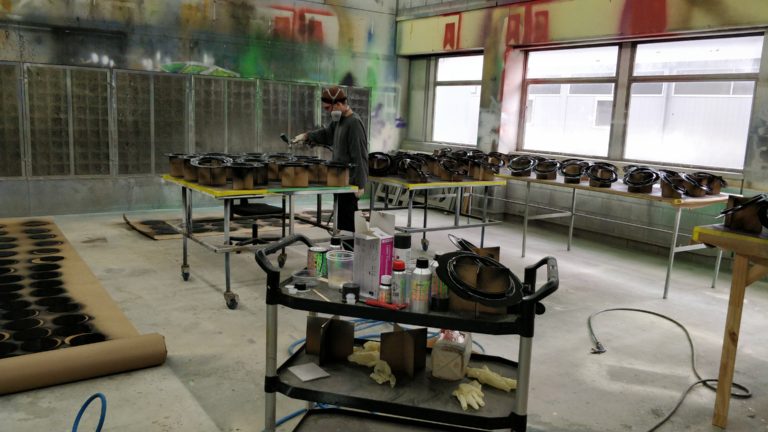
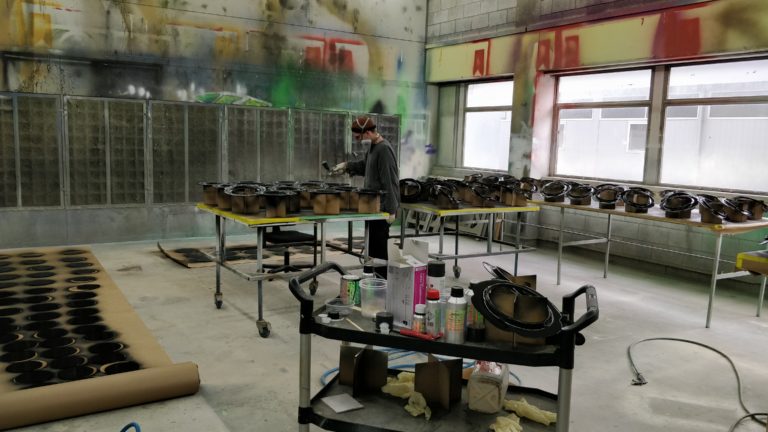
Day 5 Reflection:
- Check paints and their SDS for proper PPE use (ie. gloves, respirator, ect.)
- When using a spray gun there is only so much paint in it so keep track of how much you’re using to not run out in the middle of a part
- Cross over your spray paths for an even spray
- Do not spray too close to the part so as not to pool paint
WEEK 2
Day 6: Monday May 31st
When I arrived and sat down before the day started Joaquin came in and announced to the team that all the painting done on the casts had messed up horribly. Some of the layers had not cured between painting and they disrupted the layers above by bubbling and blooming the chrome all over the casts. Which meant we had to basically start over and get it done when time was already up. Luckily the deadline had been pushed back because of issues with the shoot but that still meant the project for Scale would be grossly over budget.
We started by everyone jumping in the bring the casts up from the spray booth to scrub all the paint off. We filled a large container with Acetone and soaked a few at a time before taking a cut down ship brush to take off the paint. All the paint was not coming off easily and the resin was starting to get soft from the Acetone eating away at it.
McGregor then suggested it would be much faster to actually recast all 70 plates instead of spending all day and some scrubbing the paint off. Joaquin and Sam gave that the green light and McGregor got to pumping them out.
I then spent the rest of the day with some help from Joaquin doing the same thing I did my first day at Scale. Cutting off the pour spouts, filing them down with a power file, and then sanding with their Festool orbital sander before filling with the superglue mix.
It was an overall stressful day for the whole crew. Not everyone could jump on to help without some tasks getting over crowded, but everyone was making sure they were working towards the completion of the recasts or another project so they would not fall behind. I unfortunately in the chaos of the day did not take any pictures.
Day 6 Reflection:
- Always make sure ample time is given for paint layers to dry and cure (especially two part mixtures in colder then average environments)
- Not working on the same task can also be beneficial to the whole team, helping keep other tasks from stacking up so everyone can get back on track
- When a large mistake like this arises it’s amazing to see everyone come together work incredibly efficiently on the problem
Day 7: Tuesday June 1st
All 70 casts were finished before the day was out on Monday so the following day was spent filling in air bubbles and imperfections before priming could happen. Sam and Cody were available to help so the entire Scale team worked our way through the 70 plates making them smooth.
Unfortunately two plates ended up with a very thin edge where the pour spout was so I had to recast them and quickly catch them up to the rest of the casts. This is where speed got the better of me and I messed up a cast so I had to in the end cast three to get two solids plates.
Day 7 Reflection:
- Always check yourself to make sure you are not putting speed above the process and safety
Day 8: Wednesday June 2nd
When I arrived Joaquin had already started priming the plates all at once instead of two batches. This is something we all agreed should be done with everything to help guarantee a more uniform paint job. However it wasn’t long after the day started that Sam got a call from the (REDACTED) production team.
They had moved the film date up from the following Friday to the day after Queen’s Birthday, the following Tuesday. Which meant the plates needed to ship out today for them to arrive on time. This really added insult to injury as there was already the money spent on the messed up plates but now they would have to change the finished job to unpainted. The (REDACTED) production correspondent said their props department could paint them for the shoot as long as they got them ASAP.
Joaquin finished priming the plates by after lunch so we all jumped on packing them out to send out that evening. After they were all packed Joaquin asked if I could continue working on a tractor handle they had been asked to remake for the Avalon grounds keeper.
I added Fantastic Filler on top of the areas Joaquin had already built up to help smooth them out. I then started sanding down to smooth working my way up to 1000 grit sandpaper. Along the way I filled in smaller areas I missed with the bog with the Superglue/Baby Powder mix. I filled the last little problem areas and it hit the end of the work day.
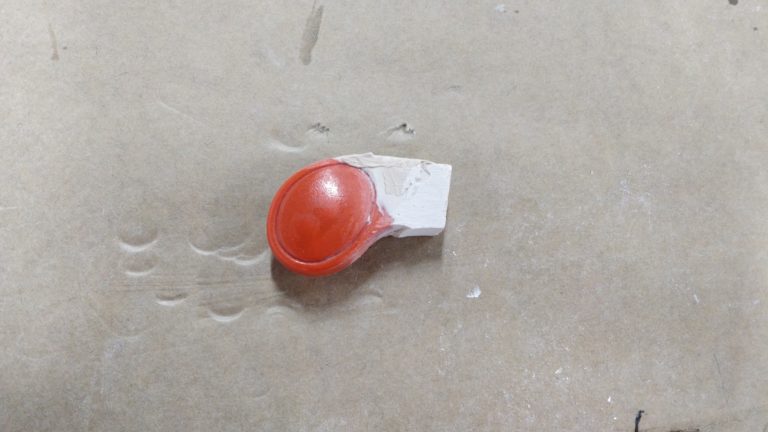
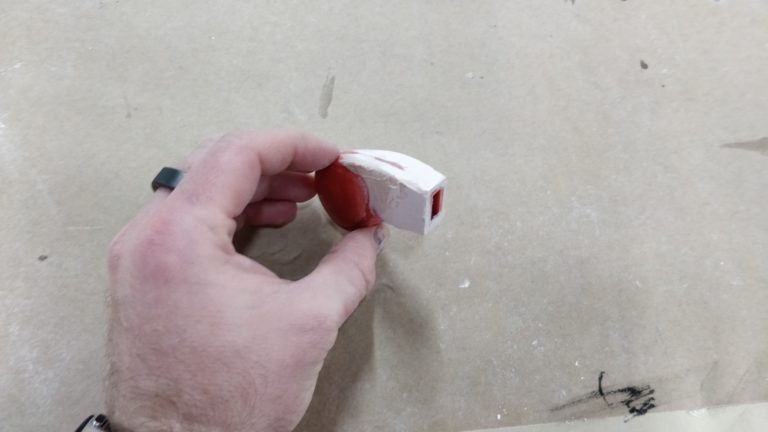
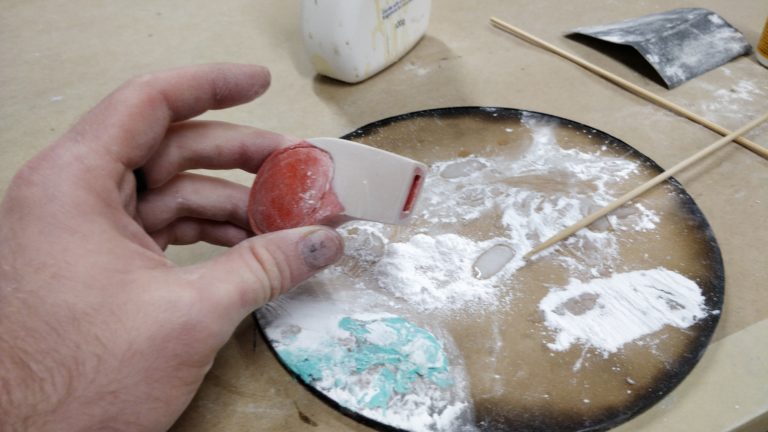
Day 8 Reflection:
- Sometimes the product has to be sent off early to meet the demands of studios/production companies’ timeline
Day 9: Thursday June 3rd
When I arrived I started back on the tractor handle doing a final pass with sandpaper to smooth out the filling I did before leaving Wednesday. After it was smooth I was shown what filler primer I should use then went to the spray booth to put a coat on the part.
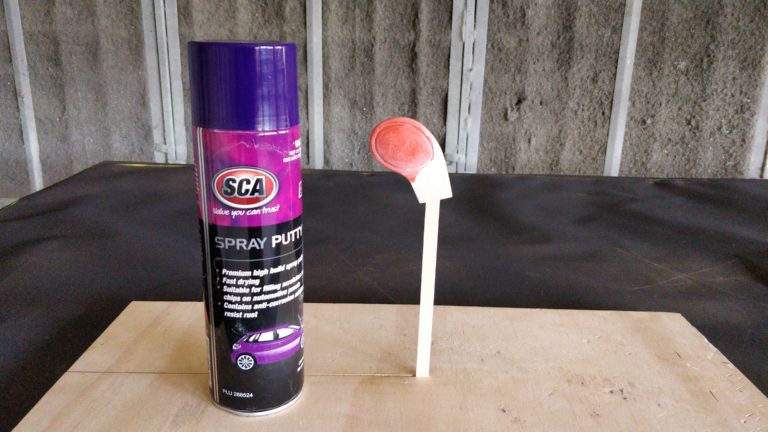
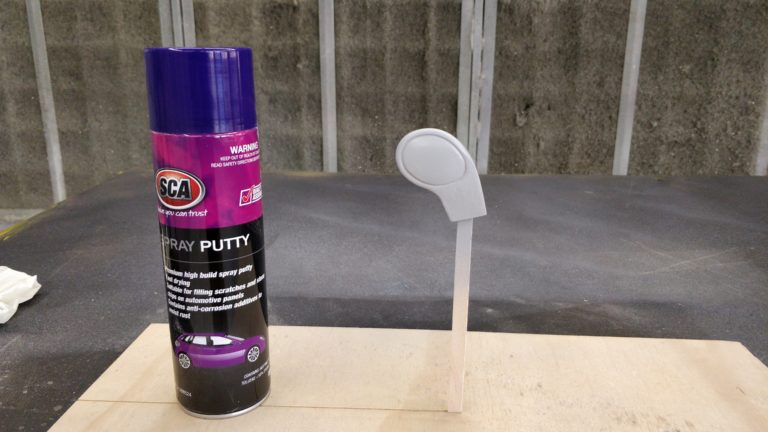
After the handle was sprayed and put in the “Goo Room” to finish drying, Scale’s new large resin printer arrived! Joaquin and Sam knowing I had previous experience with 3D printers asked me if I wanted to be in charge of finding it’s new home in the sop and setting it up. To which I replied with a ‘HECK YES’!
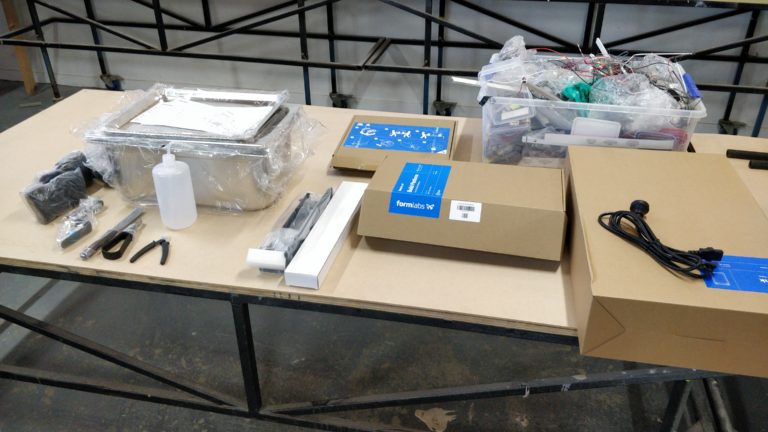
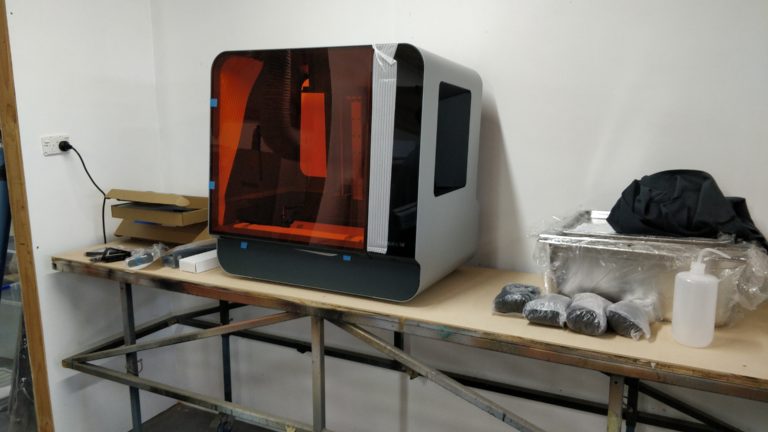
Day 9 Reflection:
- As the week and my internship were winding down I was allowed to work more on things that I enjoyed setting up/doing instead of where I was most needed
- Helping set up the new printer gave me joy in knowing I’ve helped set up a new integral part of the pipeline of making for Scale
Day 10: Friday June 4th
I reached the last day of my internship and Scale didn’t have any more projects to really work on so that meant it was a shop deep clean day.
We each split to different areas of the shop tidying up all the tool and materials to specific areas to sort out and put away. I helped sweep up a number of the areas of the dust that had built up even over the last two weeks. Some areas of the shop were totally reorganized for a better workflow and layout for use.
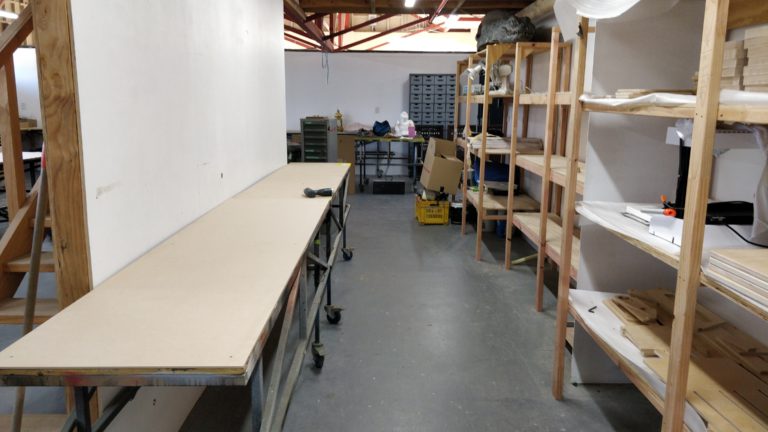

- It was an amazing experience interning at Scale and I really felt like a part of the team by the end of it
- Always clean up your workspaces before you leave every day, it makes it easier to start the following day, and keeps you from having to spend an entire day to clean all the areas of the shop that have been neglected
- I have a real love for planning/making shop organization structures as I find it relaxing to give a tool or material a home that is more efficient in the flow of the shop
- Joaquin and Sam saved up a lot of money working before deciding to start Scale
- Connections connections connections
- They make sure they are equipped to do more then just prop builds for film/television so they can have a more consistent revenue stream in down times
Working Question Reflection:
- What skills do I need to develop to become a well rounded maker in a professional space after graduation?
- I found this question had to find a specific answer to on internship since I already have at least a base in most general skills. However from talking with Joaquin and Steven during my internship then instead told me to figure out what my strength is that helps me stand out in an area. For example Steven is primarily a sculpture but has the ability to also do most general work. They said that every shop if going to hire someone for a specific area or department so it is better to have a stronger skill in one area to stand out for hirers.
- How can I leverage my current knowledge to be an asset to a new team?
- This question is also tricky to answer as it will be different for every new team I go to work with. For Scale it was having to be confident in the skills or techniques I knew how to accomplish but also being confident enough to ask for help in things I was unsure of. Checking with Sam or Joaquin in which way they do things at Scale so the finished products would have a consistent quality to them. Even if there were things I also knew how to do I had to make sure I checked my ego at the door to listen to how the process is at Scale incase I had been doing wrong all along or they had a more efficient way to get the same result.